ИЗГОТОВЛЕНИЕ РУПОРА ДЛЯ АКУСТИЧЕСКОЙ СИСТЕМЫ СВОИМИ РУКАМИ
В статье представлена технология изготовления рупора, позволяющая получить достаточно высокую точность
его геометрических размеров, и пригодная для реализации в домашних условиях.
Эта статья посвящена исключительно технологическим вопросам изготовления круглого рупора, в ней вы не
найдете ни методики расчета рупоров, ни конкретных размеров, ни расхваливания получившегося рупора, а
только как ее сделать дома, на коленках, с достаточной точностью и минимальными материальными затратами.
Предполагается, что вы имеете набор координат, задающий ее геометрию.
Почти все, что можно узнать в сети о рупорах есть на страницах сайта «Horn» - выбор
параметров, варианты конструкций, апплеты для расчетов, ссылки и многое другое. Мы отправляем всех, жаждущих
углубить свои знания в этой области, на этот сайт.
Сомнения
Итак, мы решили сделать среднечастотное звено будущей акустической системы в виде
рупора. После выбора динамической головки, расчета рупора и получения всех необходимых чертежей в Автокаде,
мы уставились на эти чертежи и крепко задумались. Как же изготовить такую большую деталь (диаметр более
полуметра), имеющую достаточно сложную форму.
Вариант изготовления рупора из сегментов был отброшен сразу. Вызывала большое сомнение
возможность обеспечить приемлемую точность геометрических размеров при использовании толстого материала
(МДФ или фанеры), а делать рупор из 3-х миллиметровой фанеры не было особого смысла. Да и хотелось все-таки
сделать его круглым. Дальше пошли полуфантастические предложения наподобие вытачивания рупора из цельной
заготовки или изготовления прессформы для литья под давлением. После зондирования вопросов о наличии соответствующего
оборудования и стоимости работ мы от этих идей быстренько отказались. Получалось, что или затраты на изготовление
нескольких экспериментальных образцов были неприемлемо велики, или возникали большие технологические трудности,
или не было подходящего оборудования.
Спустившись с небес на землю и слегка поспорив (наше любимое времяпрепровождение),
мы сошлись во мнении, что наиболее подходящим вариантом изготовления нескольких образцов – будет выклейка
рупора. Так как жесткие требования по соблюдению геометрии и качеству поверхности предъявляются к внутренней
поверхности рупора, а к наружной поверхности особых требований нет, то приняли способ выклейки на модели.
Теперь следовало решить вопрос, из чего клеить. Рассматривалось три варианта (в принципе,
все три пригодны), клееный рупор из бумаги или бумаги и ткани с использованием клея ПВА, выклеивание из
стеклоткани на полиэфирной смоле и формование из папье-маше, приготовленного на ПВА. Нам показался наиболее
технологичным именно третий вариант, очень привлекала и ничтожная стоимость исходных материалов.
Для оценки свойств материала был проведен эксперимент, в качестве модели использовался
полиэтиленовый рассекатель от большой лейки по форме очень напоминающий будущий рупор. После полного высыхания
наформованной массы мы сняли готовую детальку с импровизированной модели и пристально ее изучили. Результаты
были очень обнадеживающими, внутренняя поверхность рупора была практически без изъянов и точно повторяла
форму рассекателя, высохшее папье-маше по фактуре напоминало ДВП (но более рыхлое), было весьма прочным,
легким и «глухим». Это окончательно подвигло нас на изготовление полноразмерного рупора из папье-маше.
Проект
Как мы себе представляли конструкцию рупора и крепление к нему динамической головки,
показано на рисунке 1. Предполагалось, что динамическая го ловка крепится к фанерному фланцу, приформованному
к гор лу рупора и фактически являющимся его продолжением.
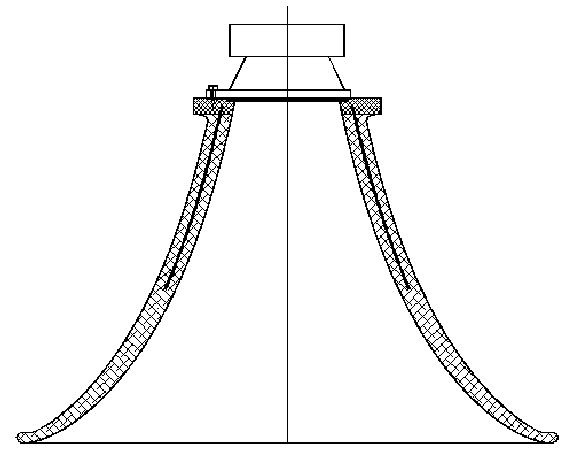
Рисунок 1
Внутренняя поверхность фланца соответствовала профилю горла рупора. Для обеспечения
достаточной механической прочности крепления фланца и армирования самого рупора во фланец должны вкручиваться
восемь резьбовых шпилек диаметром 4мм и длиной 200ч250мм, которые заформовываются в тело рупора (как показала
практика, выдернуть шпильку без разрушения рупора – невозможно).
Толщина фланца выбрана достаточно большой - порядка 20мм, с расчетом на то, чтобы
на его внешнюю поверхность можно было бы надеть и закрепить заднюю камеру. Попутно фланец используется
как элемент, за который можно стянуть готовый рупор с модели. Чертеж фланца показан на рисунке 2.
Рисунок 2
Так как рупор - тело вращения, то используя некоторое подобие гончарного круга и
точный шаблон, можно обеспечить высокую точность изготовления модели из пластичного мате риала. Вполне
достижима погрешность, не превышающая долей миллиметра. Исходя из этих соображений, был спроектирован
наш вариант приспособления для изготовления модели (Рис. 3).
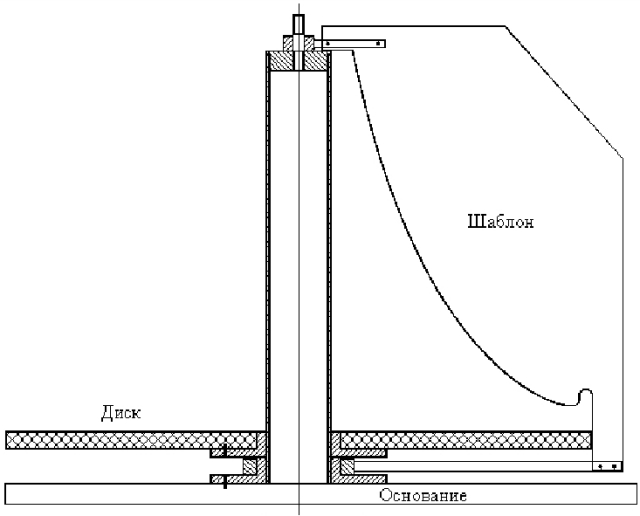
Рисунок 3
Он состоит из центральной стойки (использовали отрезок толстой трубы), на которую
снизу надеты два фланца, а сверху вставлена пробка с вкрученной металлической осью. Верхний фланец предназначен
для крепления диска, на котором будет формоваться модель, и он же обес печивает его перпендикулярность
к стойке, а нижний – для крепления всей конструкции к верста ку (в итоге, использовали кусок толстой широкой
доски). Фланцы просто лежат друг на друге.
Диск и основание крепятся к фланцам шурупами через просверленные в них отверстия.
На нижний (неподвижный) фланец и верхнюю ось надеты две втулки по скользящей посад ке, к которым приварены
поводки для крепления шаблона.
Конструкция получилась довольно удобной для работы, так как вокруг оси независимо
могут вращаться и шаблон, и диск, но несколько сложноватой. Вы можете придумать и более простую конструкцию,
например, с неподвижным шаблоном, но в любом случае необходимо выполнить два основных требования, обеспечивающих
точность изготовления модели.
Во-первых, стойка (ось вращения) должна быть перпендикулярна диску, на котором фор
муется модель. И конечно, поводки, крепящие шаблон, должны иметь достаточную жесткость.
Во-вторых, следует стремиться обеспечить минимальные люфты во вращающихся деталях.
Шаблон можно изготовить из любого тонкого (0.8ч1.5мм) и жесткого материала – дюралюминия,
стали, стеклотекстолита.
Фактически, обращение к внешней помощи требуется только при изготовлении фанерного
фланца и приспособления для формования модели (требуется токарная обработка). Если это вы зывает непреодолимые
сложности, то в принципе, можно обойтись и собственными силами.
Фланец можно выпилить лобзиком, а для формования модели использовать конструкцию
с непод вижным шаблоном. В этом случае шаблон и центральная стойка жестко и перпендикулярно кре пятся
к нижнему основанию, а диск надет на стойку и лежит прямо на основании (для облегчения вращения диска
целесообразно проложить между ними прокладку из тонкой и скользкой пласт массы).
Ценные указания
Несмотря на полушутливое название этого раздела, в нем есть доля истины. Так как
в даль нейшем основные работы по изготовлению рупора будут связаны со шпатлеванием, ошкуривани ем и покраской,
то чтобы многократно не повторяться, мы позволим себе дать несколько советов по выполнению этих работ
и выбору материалов. Профессиональные маляры могут этот раздел сразу пропустить, но для тех, кто знаком
с малярными делами исключительно по покраске окон и дверей, он может быть полезен.
• Во-первых, следует использовать только качественные материалы
известных марок. Это необходимо для их правильного применения и проверки на предмет совместимости (на
пример, на некоторые марки шпатлевок плохо ложатся синтетические эмали). В общем, идя в магазин покупать
материалы – смотрите, что написано в инструкциях по применению.
При выполнении грубых работ мы, в основном, использовали гипс и водорастворимые шпатлевки
на основе гипсового вяжущего (наилучшей, можно считать шпатлевку для гип сокартонных плит с торговым названием
– «Изогипс»). Для более тонких операций исполь зовались также водорастворимые акриловые шпатлевки – стартовая
и финишная. Эти шпатлевки практически не имеют запаха, отлично шлифуются всухую, имеют достаточно
твердую поверхность и допускают нанесение практически любых красок. Из лакокрасоч ных материалов использовались:
натуральная подсолнечная олифа, глифталевый или пен тафталевый лак с любым номером, начинающимся на 1
(признак устойчивости к атмосфер ным воздействиям) и пентафталевая эмаль типа ПФ115 для выполнения промежуточных
операций окраски. Для финишной окраски желательно использовать высококачественную импортную масляно-фталевую
синтетическую эмаль холодной сушки, обладающей свойст вом самовыравнивания, и наносить ее распылением.
Удовлетворительные результаты так же можно получить, используя для финишной окраски декоративные алкидные
эмали в аэ розольной упаковке.
• Во-вторых, каждая следующая операция по обработке заготовок
выполняется только после полного высыхания нанесенных ранее покрытий.
• В-третьих, при выполнении шпатлевки никогда не пытайтесь исправить
замеченные дефек ты на только что прошпаклеванной поверхности, дайте шпатлевке высохнуть, ошкурьте поверхность,
и тогда исправляйте. В противном случае, подсохшая шпатлевка потянется за шпателем, и вы получите лунную
поверхность вместо нескольких небольших дефектов, усилий на ее ошкуривание уйдет раз в десять больше.
При шпатлевании придерживайтесь принципа – лучше десять впадин, чем один бугор. Вы потратите гораздо больше
времени на сведения со света этого бугра, чем на повторное шпатлевание.
• В-четвертых, каждая следующая операция по доводке поверхности
до желаемого качества начинается с ошкуривания, это правило относится и к многослойным лакокрасочным по
крытиям (в том числе и на финишных этапах покраски). Для ошкуривания удобно исполь зовать сетчатую шкурку,
для грубой обработки применяются шкурки с зернистостью 60ч200, для финишной обработки используется шкурка
с зернистостью 400ч500. Запаси тесь достаточным количеством шкурки, за время работы над рупорами вы с
ней сродни тесь.
• В-пятых, после ошкуривания и перед началом нанесения следующего
слоя покрытия деталь следует тщательно обеспылить.
• В-шестых, после завершения очередного этапа работы тщательно
отмойте инструмент. Прекрасно смываемые водой сырые шпатлевки ни в какую не хотят удаляться после высы
хания, ну о кистях и нечего говорить – не отмытую кисть придется просто выбросить.
В заключение этого раздела хотим мы также вам заметить, что итог вашей работы по
изготовле нию рупора на 99% зависит от вашей аккуратности и терпения.
Изготовление модели
Описанное выше приспособление для изготовления модели (Рис.3) содержит две детали,
которые необходимо изготовить самостоятельно, это диск и шаблон. Диск вырезается электролоб зиком (можно
и руками) из куска ДСП толщиной 16мм. Диаметр диска должен превышать макси Copyright © 2004 NexTube All
Rights Reserved 5 мальный диаметр модели на 40ч50мм. Этот припуск необходим из-за усадки папье-маше, надо
сознательно сделать диаметр плоской части рупора (там, где устье рупора переходит в плоскость ему перпендикулярную),
чтобы потом подрезать его в размер. Мы попытались завершить устье буртиком, он хорошо заметен на шаблоне,
и этот буртик сыграл с нами злую шутку, более под робно мы коснемся этого вопроса позже.
Для защиты диска от влаги, для исключения коробления он дважды пропитывается подогретой
олифой. Олифу наносят на рабочую (ту, где будет формироваться модель) и торцевую поверх ность диска широкой,
мягкой кистью до тех пор, пока олифа не перестанет прямо на глазах впи тываться. Через пару дней операцию
повторяют. Олифу подогревают на водяной бане, проще го воря, ставят емкость с олифой (желательно металлическую)
в кипящую воду и выжидают минут 15. Емкость с олифой необходимо чем-нибудь прикрыть, иначе пары олифы
могут вспыхнуть. Ни в коем случае не пытайтесь нагреть олифу прямо на огне, это опасное мероприятие –
горячая оли фа чрезвычайно горюча. Еще через пару дней диск покрывается одним слоем лака.
Пока это все сохнет можно заняться изготовлением шаблона. Так как мы имели все черте
жи в Автокаде, то чертеж был выведен в масштабе 1:1 на принтер. Полученный лист бумаги на клеили на кусок
стеклотекстолита клеем, не размягчающим бумагу (использовали клей «Мо мент»), и обработали по контуру.
Затем грубо придали форму шаблону, обрезая материал ножов кой по металлу, рабочая поверхность (задающая
форму рупора) доводилась напильниками и наж дачной бумагой.
Если вы имеете набор координат образующей рупора, то также целесообразно выполнить
все по строения на листе бумаги и наклеить ее на лист, предназначенный для изготовления шаблона. Ес тественно,
надо стремиться делать все максимально точно. После обработки шаблона по контуру надо одну из кромок рабочей
поверхности скосить под углом 30ч45 градусов, вторая кромка по страдать не должна. Шаблон становится несимметричным,
при формировании поверхности его надо вращать только в одну сторону так, чтобы скошенная кромка набегала
на поверхность моде ли.
При проектировании шаблона целесообразно сделать его так, чтобы верхняя точка линии,
задаю щей форму рупора, совпадала по высоте с верхней кромкой стойки, это существенно облегчает его установку,
и под нижней точкой этой линии оставалось 15ч20мм до поверхности диска.
Для удобства работы, чтобы на начальных этапах работы наносимый материал не сползал
с диска, по контуру диска прибивается металлическая обечайка (на рисунке не показана). Ее высота приблизительно
равна половине зазора между шаблоном и диском, для ее изготовления использо вались обрезки кровельного
железа.
Приспособление собирают, и тщательно юстируют положение шаблона относительно оси
вращения.
Теперь, собственно говоря, начинается изготовление модели.
Этап 1 – заполнение внутреннего объема модели.
Для заполнения внутреннего объема модели можно использовать любой материал – от кусков
де рева до глины и цементного раствора. В итоге, необходимо получить грубое подобие рупора, зазор между
заполнителем и шаблоном должен составлять 3ч15мм.
Мы использовали смесь мелкого керамзита (для облегчения веса) со строительным гипсом
в соот ношении 2:1 по объему. Смесь готовится небольшими порциями в широкой мягкой посудине (по том легко
удалять засохшие остатки гипса слегка ее помяв), сначала смесь перемешивается в сухую, потом затворяется
водой, повторно перемешивается и вываливается на диск. Форму смеси придают, разравнивая ее шпателем, проделывать
все надо быстро – время жизни смеси 4ч5 минут.
Необходимо постоянно контролировать толщину нанесенной смеси шаблоном. Не пытайтесь
сдвигать смесь шаблоном, она для этого чересчур жесткая и шаблон может потерять юстировку. Выступающие
участки сдвигают или удаляют шпателем. В верхней части рупора и под шаблоном получается слишком маленький
зазор, чтобы использовать смесь с керамзитом, эти участки запол нялись чистым гипсом. Процедура заполнения
внутреннего объема выполняется за один раз без перерывов.
После первого этапа модель представляла душераздирающее зрелище и напоминала большую
ку чу белого…, сами догадайтесь, чего.
Этап 2 – формирование поверхности модели.
На этом этапе с помощью шпатлевки на основе гипсового вяжущего, производится основное
фор мирование поверхности модели, теперь уже - шаблоном. Затворите шпатлевку водой и тщательно Copyright
© 2004 NexTube All Rights Reserved 6 перемешайте с помощью механической мешалки, вставленной в дрель.
Консистенция шпатлевки должна напоминать очень густую сметану. С помощью ракеля (резинового шпателя),
нанесите толстый слой шпатлевки на модель и разравнивайте его шаблоном, сдвигая его в одну сторону.
Перед шаблоном образуется как бы валик из шпатлевки, когда он станет тонким или появятся
пропуски в шпатлевке, наносите очередную порцию шпатлевки. Желательно так рассчитать нано симое количество
шпатлевки, чтобы, когда вы полностью обойдете шаблоном модель, перед шаб лоном шпатлевки практически не
было.
Возможно, вам придется проделать эту операцию еще один раз (естественно, после высы
хания предыдущего слоя), все зависит от вашей квалификации. Перед началом работы проверьте, свободно ли
вращается шаблон вокруг модели, если он цепляется за выступы – удалите их.
При ошкуривания модели как держатель шкурки удобно использовать кусок толстой резины
(8ч10 мм) средней твердости, шкурка оборачивается вокруг резины. Шкурить модель, прижимая шкурку рукой,
нежелательно, это может привести к образованию неровностей.
После этого этапа работы модель уже практически полностью соответствует заданной
форме.
Этап 3 – черновая доводка поверхности.
Возможно, если предыдущий этап работы выполнен тщательно, он вам и не потребуется.
Факти чески, это повторение этапа 2, только с использованием стартовой акриловой шпатлевки.
После этого этапа работы шаблон должен без зазоров, с легким трением скользить по
поверхности
модели
Этап 4 – защита модели от влаги.
Поверхность модели следует тщательно защитить от воздействия влаги, для этой цели
поверх ность модели пропитывается горячей олифой.
Этап 5 - финишная доводка поверхности.
Сначала необходимо удалить шаблон, проверку соответствия поверхности модели заданной
фор ме, в случае необходимости, осуществляют прикладыванием шаблона.
Первоначально, поверхность модели окрашивается так называемым проявочным слоем краски.
Цвет краски должен быть достаточно контрастен цвету шпатлевки. После ошкуривания поверхности мелкой шкуркой
(зернистость - 300ч400), вы увидите на поверхности массу мелких дефектов – царапины от шаблона, крупинки
шпатлевки, следы от шкурки. Все замеченные дефек ты шпатлюются финишной акриловой шпатлевкой.
Далее цикл повторяется – ошкуривание, покраска, ошкуривание и повторный контроль
по верхности на наличие дефектов. Если поверхность равномерно матовая, не имеет видимых дефек тов и при
проведении по ней рукой не ощущаются неровности – этап завершен. Если вы не удов летворены результатами
– цикл работы повторяется, нам хватило трех заходов.
Это очень важный этап работы, следует учесть, что поверхность контакта отформованного
рупора с моделью имеет очень большую величину, и неровности поверхности модели сильно за трудняют его
снятие. При небрежном выполнении работы вы просто не сможете снять готовый рупор без разрушения модели,
а сделать вам надо, как минимум, две штуки.
Этап 6 – окраска модели.
Поверхность модели дважды окрашивается пентафталевой эмалью.
Этап 7 – нанесение разделительного покрытия.
Для облегчения снятия готового рупора с модели и дополнительной защиты модели от
влаги ее поверхность покрывается разделительным слоем. В качестве разделительного слоя можно исполь зовать
восковую мастику для пола, но нам не удалось обнаружить ее в продаже.
Поэтому мы изготовили мастику самостоятельно. После некоторых раздумий мы пришли
к выво ду, что это к лучшему – точно известно, что используется. Мастика готовится из скипидара и на турального
воска, смешанных в соотношении 2:1 (по массе). Мастика приготавливается следую щим образом: в подогретый
на водяной бане скипидар тонкой струйкой вливается расплавленный воск при непрерывном перемешивании. Остывшую
мастику наносят на поверхность модели мяг кой кистью тремя толстыми слоями (с промежуточной сушкой каждого),
последний слой аккурат но располировывается суконкой.
На этом изготовление и подготовка модели заканчивается. На рисунках 4 и 5 показан
ито говый результат наших трудов.
Приготовление папье-маше
Эту работу целесообразно делать параллельно с изготовлением модели. У вас будет доста
точно времени для этого из-за вынужденных перерывов в работе, необходимых для полного вы сыхания очередного
слоя шпатлевки.
Для приготовления папье-маше подходит бумага газетного качества, мы использовали
ка кие-то старые журналы. Для начала, необходимо определить необходимое количество бумажной массы. Ориентировочно,
определить необходимый объем можно, аппроксимировав рупор двумя усеченными конусами по наружной и внутренней
поверхности (предварительно задайтесь толщи ной стенки). Разница объемов этих конусов и даст искомую величину.
На изготовление нашего рупора потребовалась 2/3 десятилитрового ведра бумажной массы.
Итак, заготовленную бумагу необходимо порезать (порубить, покромсать, порвать на
клоч ки – это уже в самом конце процесса) на небольшие кусочки (10х10 ч 20х20 мм). Скажу честно, процесс
резки чрезвычайно нудный, после первого журнала возникло непреодолимое желание его механизировать, установив
вместо циркулярной пилы мелкозубую фрезу, журналы стали резать целиком. Резаная бумага замачивается в
воде (воды должно быть с избытком), и оставляется для набухания на 5ч6 дней. Каких-либо антисептиков в
замоченную бумагу мы не добавляли.
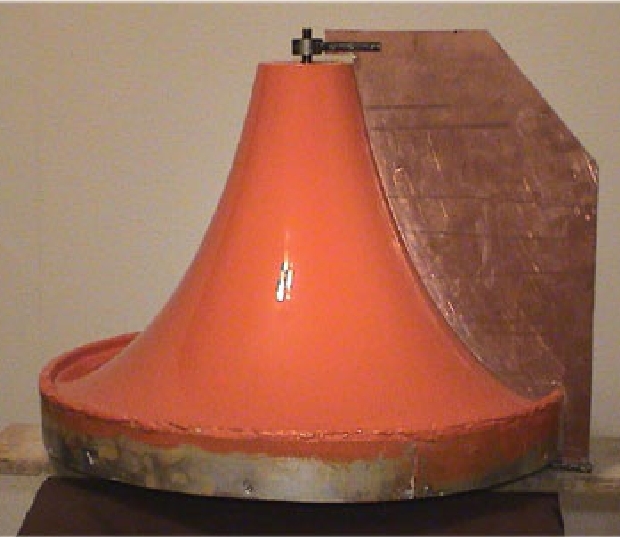
Рисунок 4
После набухания просто куски мокрой и мерзко выглядевшей бумаги надо превратить
в однородную бумажную массу. Это удобно проделывать в толстостенном пластмассовом ведре с по мощью вращающегося
ножа, вставленного в дрель. Ведро следует заполнить резаной бумагой примерно до половины и еще добавить
воды. Если воды будет мало, процедура будет мучительно долгой и безрезультатной.
В качестве ножа сначала использовался нож от старой кофемолки, накрученный на длинный
стержень; так как стержень был тонковат, на него был надет отрезок трубки подходящего диаметра, он выполнял
роль подшипника и при работе придерживался рукой. Для такого использования нож от кофемолки оказался слабоват,
у него постоянно норовили скрутиться режущие плоскости. По его подобию был изготовлен более массивный
нож, к 8-ми миллиметровому прутку была приварена стальная пластинка длиной 100мм, у которой края были
загнуты вверх и заточена режущая кромка. Можно попробовать использовать строительную мешалку, заточив
кромки у спиральных лепестков.
Нож опускается в ведро, дрель включается, и бумага рубится до тех пор, пока масса
в ведре не станет смахивать на пюре. Готовую массу следует хорошо отжать, операция проделывалась очень
просто – масса зачерпывалась рукой и отжималась в горсти (сколько сил хватало), после чего складировалась
в другую емкость. Конечно, работа сопровождалась мыслью о механизации: пресс какой-нибудь, но мысль была
не додумана – масса быстро закончилась.
Непосредственно перед формованием рупора в бумажную массу вводится клей ПВА, при
близительно 12ч20% от объема бумажной массы. У нас ушло приблизительно 1.2л клея.
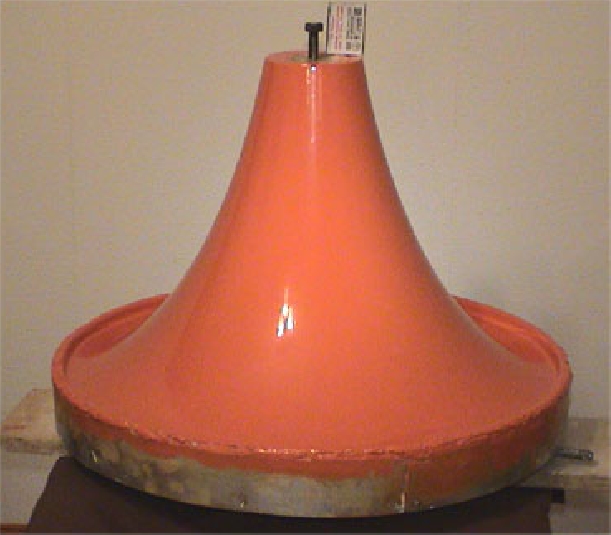
Рисунок 5
Бумажная масса с введенным клеем тщательно перемешивается мешалкой, вставленной
в дрель. Пальцы после сжатия комка бумажной массы в руке должны оставаться слегка липкими. После высыхания
папье-маше дает усадку порядка 5ч10%, это надо учитывать при выборе всех внешних размеров и толщины стенок
рупора.
Формование рупора
Перед началом формования рупора необходимо изготовить три дополнительные детали и
подготовить фланец.
Во-первых, надо сделать еще один шаблон, его основное назначение – обеспечить заданную
тол щину стенок рупора. Никаких особых требований к его точности, да собственно, и к форме, не предъявляется.
Как он выглядит и устанавливается, показано на рисунке 6.
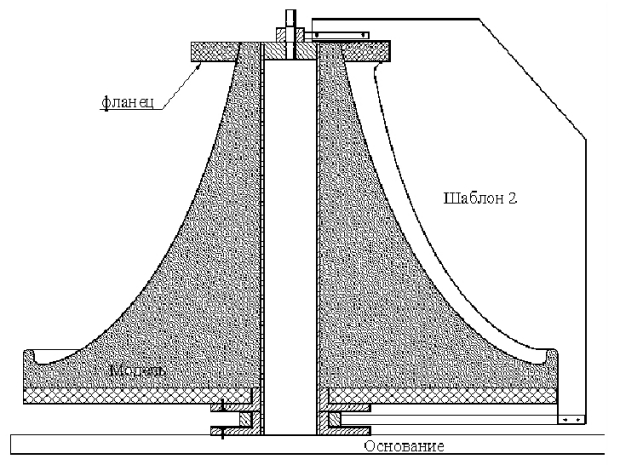
Рисунок 6
Толщина стенок рупора принята не одинаковой: в районе устья толщина стенки равна
15мм и плавно увеличивается к горлу рупора до 30мм. Увеличение толщины стенки продиктовано тем, что в
верхней части находятся закладные детали и в районе крепления фланца требуется большая механическая прочность.
Во-вторых, необходимо изготовить две накладки – верхнюю и нижнюю (Рис 7.) Верхняя
накладка вырезается из куска ДСП и прикручивается шурупами к фланцу. Своей центральной частью она упирается
в стойку и не дает сместиться фланцу вниз при высыхании папье-маше.
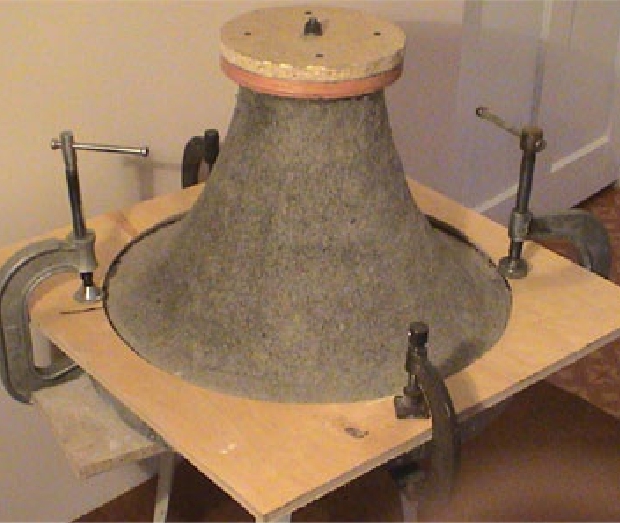 Рисунок 7
Нижняя накладка вырезается из 10мм фанеры и пред ставляет квадрат с вырезанным по
центру отверстием, равным максимальному расчетному диаметру устья рупора. Ее основное назначение: прижать
нижний край рупора к модели и не дать ему подняться в процессе высыхания.
Подготовка фланца заключается во вкручивании (лучше на клею) в него отрезков 4мм
резьбовых шпилек (покупная деталь) и изгибании их так, чтобы они были приблизительно параллельны образующей
рупора.
Резьба была нарезана прямо в фанере механическим метчиком, шпильки изгибались рукой.
После этого можно начинать формование рупора. Мы лепили рупор в четыре руки, весь процесс занял минут
двадцать. Бумажная масса с введенным кле ем расплющивается на ладони и этими лепешками оклеивается поверхность
модели. Масса, нанесенная на модель, тщательно разравнивается и уплотняется ладонями. После нанесения
первого слоя толщиной мил лиметров 10 на горло модели надевается фланец и ус танавливается шаблон. Шпильки
по кругу обвязыва ются несколько раз мягкой стальной проволокой, и формование рупора продолжается. Толщина
нанесен ной массы контролируется шаблоном. На заключи тельных этапах формования бумажная масса прикатывалась
небольшим резиновым валиком. После завершения формования шаблон снимается и прикручивается верхняя накладка,
потом сверху надевается нижняя накладка, которая прижимается к поверхности рупора. Мы использовали струбцины,
это оказалось не очень удобным, так как из-за усадки при высыхании их надо поджи мать. Наверное, удобнее
будет положить на накладку груз, например, четыре кирпича по углам.
В работе наступает длительный перерыв, до полного высыхания рупор трогать нельзя.
Наш рупор сох почти месяц. Это время можно провести с пользой – размышляя о том, как все будет (или должно)
великолепно звучать.
Снятие рупора с модели
И вот настал долгожданный и волнительный момент. Рупор высох, и его можно снимать.
Сначала были сделаны робкие попытки снять рупор руками – рупор сидел мертво и даже не ше лохнулся. Легкое
обстукивание рупора киянкой тоже не дало результатов, и в ход пошла тяжелая артиллерия. Из гаража был
притащен большой съемник, его лапы завели за фланец, а болт уперли в стойку (Рис. 8). С замиранием сердца
начали тянуть, обстукивая рупор киянкой, по мере натяги вания винта вытягивались и наши физиономии. Рупор
был неподвижен, как скала. Поскольку нам терять было нечего, решили тянуть, пока что-нибудь не поломается.
Понадобилось всего еще несколько оборотов винта и рупор соскочил с модели, радости нашей не было предела.
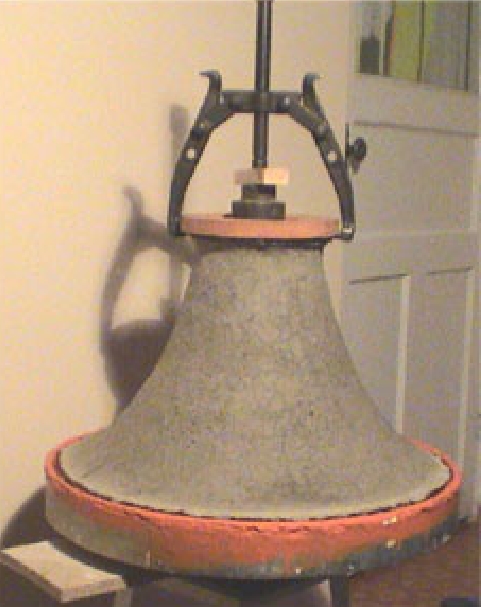
Рисунок 8
Естественно, мы бросились рассматривать, что по лучилось.
Внутренняя поверхность рупора была практически без изъ янов и точно повторяла форму
модели, сама модель полу чила незначительные повреждения – у горла рупора были сорваны небольшие участки
краски вместе с верхним сло ем шпатлевки. В общем, ничего страшного, после незначи тельного ремонта модель
можно было использовать по вторно.
Рупор получился легким и механически прочным. Как выглядит рупор до окончательной
обработки показано
на рисунке 9.
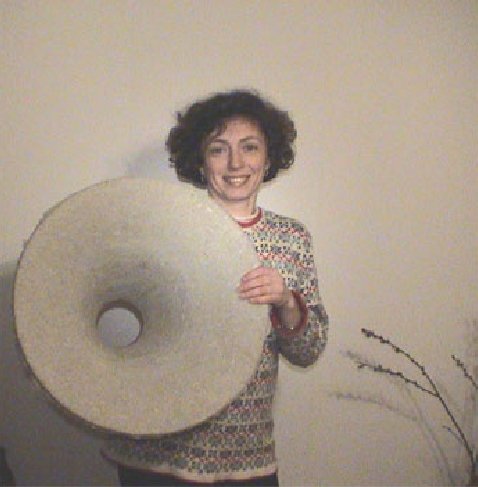
Рисунок 9
Отделка поверхности рупора
Основное внимание было уделено обработке и от делке внутренней поверхности рупора,
так как рупор изго тавливался исключительно в экспериментальных целях, наружная поверхность была просто
окрашена без всякой обработки.
Этап – 1: механическая обработка.
Сначала механически обрабатываются края устья рупора, крупные неровности срезаются
острым ножом, оконча тельная доводка формы края производится крупнозерни стой шкуркой.
Этап – 2: защита от влаги.
После этого необходимо защитить рупор от воздействия влаги, папье-маше весьма гигроскопично.
Для этого по верхность рупора пропитывается масляным лаком. Перед пропиткой внутренняя поверхность рупора
слегка ошкури вается крупнозернистой шкуркой (зернистость – 10) для удаления пленки клея. Лак разжижают
соответствующим растворителем (добавляется около 20% от объема лака) и подогревают на водяной бане. Пропитку
ведут до прекращения впитывания лака (внутренняя поверхность впитывает лак гораздо сильнее, чем наружная).
Когда мы пропитывали рупор, он совершенно бесследно впитал граммов 400 лака, возможно, впиталось бы и
больше, но закончился лак.
Этап – 3: стартовая обработка внутренней поверхности.
Для устранения мелких изъянов внутренней поверхности производится ее сплошная шпатлевка
стартовой акриловой шпатлевкой. Шпатлевка производится ракелем, в районе горла рупора для использования
ракеля недостаточно места и слишком большая кривизна, здесь поверхность шпат люется небольшим кусочком
жесткой резины. Для изготовления мини-ракеля используется жест кая резина толщиной 3ч4 мм, рабочая кромка
формируется стачиванием на наждачном камне.
Для ошкуривания поверхности рупора удобно использовать несколько кусков толстой резины
разной ширины, обернутые шкуркой, ширина куска выбирается таким образом, чтобы шкурка прилегала к рупору
всей поверхностью (достаточно трех кусков – для устья, средней части и гор ла).
Этап – 4: финишная обработка внутренней поверхности.
Поверхность рупора окрашивается проявочным слоем краски (желательно использовать
краску нейтральных серых оттенков), после ошкуривания производится шпатлевание выявленных дефек тов финишной
акриловой шпатлевкой. Так как исходная поверхность рупора имела достаточно высокое качество, оказалось
достаточным проделать эту операцию один раз.
Этап – 5: финишная окраска.
Если вас удовлетворяет качество внутренней поверхности рупора, производится финишная
окра ска синтетической эмалью в два слоя.
Вид готового рупора показан на рисунках 10 и 11. Поверхность получилась достаточно
вы сокого качества. Те, кто не знал технологии изготовления, предполагали, что рупор выдавлен или
отлит из пластмассы.
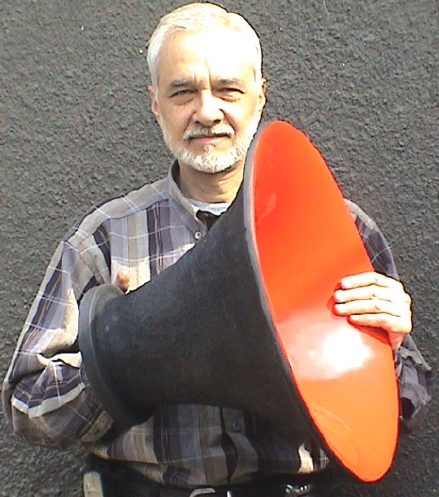
Рисунок 10
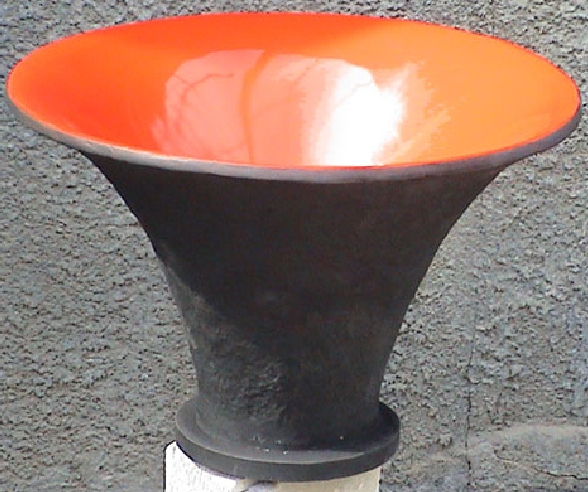
Рисунок 11
Разбор полетов
Теперь пришло время коснуться ошибок, которые мы допустили при изготовлении рупора,
и предостеречь вас.
К модели особых претензий не было, единственным ее недостатком оказался вес. Хотя
мы использовали керамзит, вся конструкция весила килограммов 30. Хотя это и не очень много, но учитывая
значительные размеры модели, такой вес создавал определенные неудобства при пере носке. По-видимому, центральную
часть модели следует заполнить более легким материалом, вроде пенопласта, а поверх него нанести гипс толщиной
20ч30мм. Такая толщина гипса обеспечит достаточную механическую прочность.
Более неприятным оказался вопрос буртика. Мы недооценили величину усадки бумажной
массы, в результате, при высыхании массы на некоторых участках край рупора ушел под буртик, и исчезла
возможность придавить его к поверхности модели (нижняя накладка легла на буртик).
Это привело к незначительным отклонениям в профиле устья рупора, на картинках этого
увидеть нельзя, отклонения слишком малы, но прецедент имеется. Поэтому мы рекомендуем не использо вать
буртик на крае устья вообще, либо сделать его гораздо меньшей высоты.
Еще одной проблемой, с которой мы столкнулись, оказался фланец. В результате усадки
папье-маше между телом рупора и фланцем образовался зазор порядка 5мм. Наши расчеты на то, что шпильки,
проходящие сквозь бумажную массу, ее удержат, оказались ошибочными. Вопрос с устранением щели решился
просто, она была заполнена акриловым герметиком, излишки которого после высыхания были срезаны острым
ножом. Возможно, решением этой проблемы будет отказ от установки фланца на этапе формования рупора. В
этом случае верхнюю накладку можно использовать как кондуктор, задающий ориентацию шпилек. После высыхания
рупор подрезается
до нужной высоты и устанавливается фланец, но в этом случае могут возникнуть трудности с правильной установкой
фланца. Так что, возможно, лучше оставить все как есть, тем более, что щель просто устранить.
Заключение
Несомненными достоинствами описанной технологии является возможность получить не
сколько одинаковых рупоров, имеющих достаточно высокую точность образующей, и низкая стоимость применяемых
материалов, а главным недостатком – высокая трудоемкость.
В статье мы попытались максимально подробно описать все этапы работы с расчетом на
то, чтобы человек, умеющий (и желающий) работать руками, но не имеющий достаточного опыта, смог проделать
весь путь с минимальными ошибками. Вам представлены уже проверенные реше ния. На самом деле не все проходило
гладко, и некоторые вещи приходилось переделывать не сколько раз.
Подводя итог, можно сказать, что мы остались довольны как внешним видом изготовлен
ного рупора, так и результатами его акустических испытаний.
УДАЧНОЙ ВАМ РАБОТЫ!
Евгений Карпов, Александр Найденко
Адрес администрации сайта: admin@soundbarrel.ru
НЕ НАШЕЛ, ЧТО ИСКАЛ? ПОГУГЛИ:
СТРОКА ПОЛЬЗОВАТЕЛЬСКОГО ПОИСКА
|
|